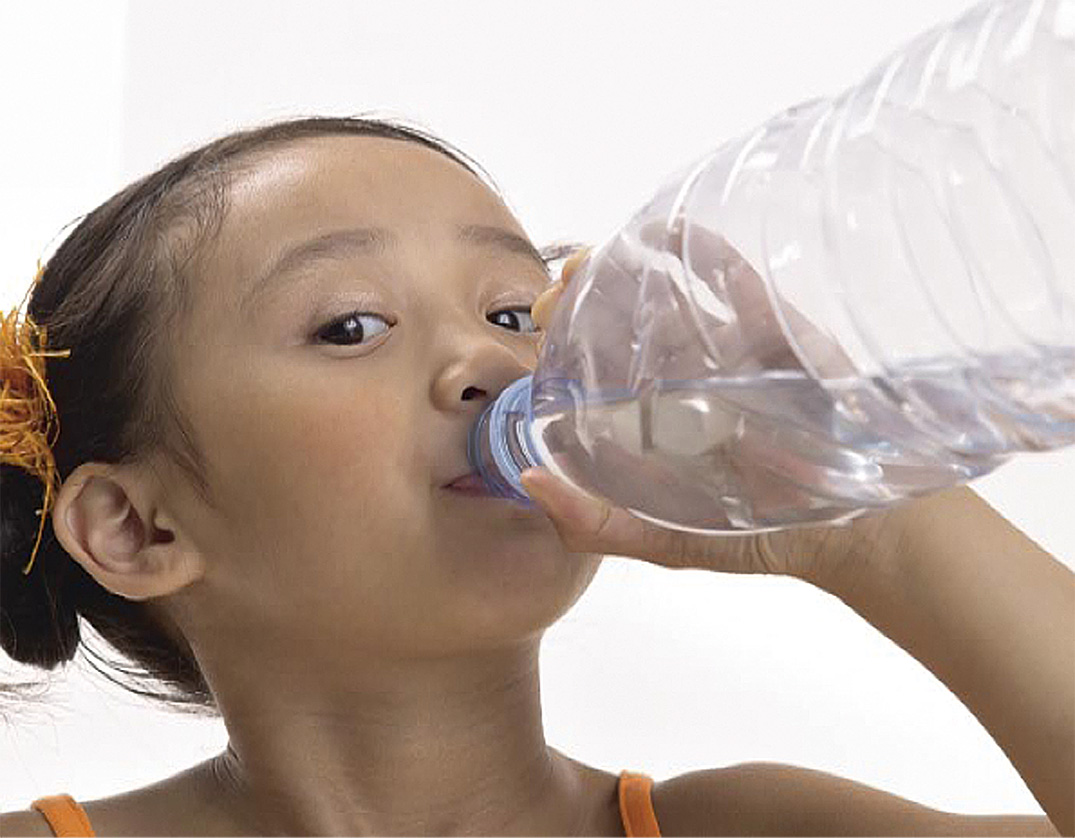
(NL/4006584916) Diez, im September 2013 In der Kunststoffverarbeitung spielt beim Thermoformen die Homogenität, die Stabilität und die Präzision der Temperatur eine Schlüsselrolle in der Herstellung qualitativ hochwertiger Produkte. Die DR. FISCHER GRUPPE hat speziell für die industriellen Prozesse des Thermoformens die LRP-Reflektorserie entwickelt, welche durch ein patentiertes Reflektorelement den Energieverbrauch um rund 40 Prozent senkt. Zudem ist es durch einen Helligkeitsregler möglich, die gewünschte Temperatur bei der Plastikverarbeitung exakt einzustellen, sodass das Objekt fehlerfrei, präzise und schnell hergestellt werden kann, so Dietmar Kegler, Geschäftsführer der DR. FISCHER GRUPPE.
Die Infrarot-Halogenlampen werden heute kontinuierlich im Werk in Pont-à -Mousson, Frankreich, produziert und basieren auf einer verbesserten HeLeN-Technologie. Diese emittiert Wärmestrahlen, die den wärmenden Eigenschaften des Sonnenlichts nahe kommen. Das patentierte Reflektorsystem LRP (Lamp Reflector Proximity) zeichnet sich durch den sehr robusten Aufbau und die dadurch bedingte deutlich höhere Lebensdauer von mindestens 5.000 Stunden aus. Durch den Einsatz von neuartigen Bauteilen wie einer Quartz-Sonde, den patentierten Reflektorelementen und einer Abschlusskappe, überzeugt das Produkt durch eine erhöhte und definierte Strahlungsdichte.
Einsatz beim Streck- und Spritzblasen
Die Infrarotlampensysteme werden beispielsweise in Streckspritzmaschinen eingesetzt, welche bis zu 35.000 PET-Flaschen pro Stunde herstellen. Bei dem Produktionsprozess werden die Polymere für die Vorformlinge (Preform) auf rund 120 Grad vortemperiert, um ihre Viskosität für das Streckblasen vorzubereiten. In diesem Vorgang kommen die Infrarotlampen zum Einsatz, welche für die nötige Erwärmung sorgen. Die Polymere werden in einen Heißkanalverteiler geführt, in welchem das Polymer mit Düsen in eine hohle, beheizte Vorform eingespritzt wird. Diese Vorform bildet die äußere Silhouette und wird anschließend um einen Kernstab eingespannt, der die innere Gestalt des Vorformlings bildet.
Durch die individuelle, präzise Einstellbarkeit der Wärmezufuhr garantieren die Produkte der DR. FISCHER-GRUPPE optimale Ergebnisse mit minimalen Produktionsausschuss. Die konstante, stabile Wärmeabgabe reduziert die Durchlaufzeiten und ermöglicht deutlich höhere Prozessgeschwindigkeiten. Die Kunststoffdicke zeigt einen besseren Temperaturgradienten und damit eine homogenere Materialtemperatur, ein Schlüsselfaktor bei der Kunststoffverarbeitung. Ist die benötigte Temperatur erreicht, wird sie durch schlichtes Dimmen der Infrarot-Lampe stabilisiert oder geregelt. Der Produktionsprozess wird damit deutlich exakter und flexibler.
Weitere Informationen unter:
http://www.profil-marketing.com